Pre-harvest checks: the need for a health and safety mindset
Ahead of harvest, Gavin Lane, CLA Vice President and Chair of the Farm Safety Partnership, finds out how two CLA members tackle health and safety on their farms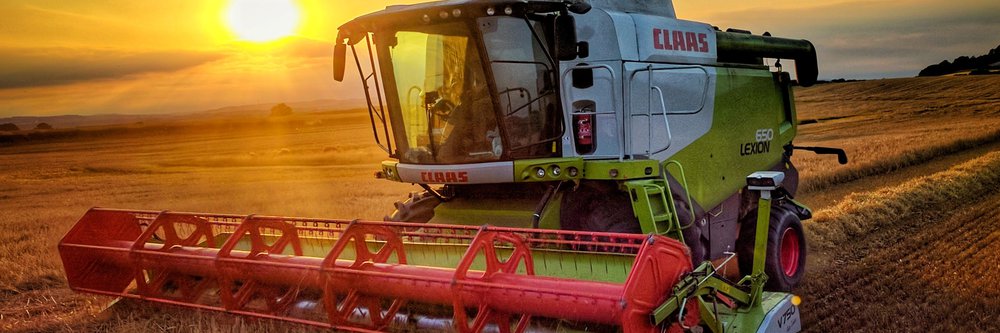
One of the most depressing aspects of chairing the Farm Safety Partnership is the link to the Health and Safety Executive’s initial fatal notification emails. The last email received was particularly heartbreaking as it outlined the death of a one-year-old child killed in a farm yard when run over by a tractor and trailer. The devastation reaped on the family of this child is hard to imagine, and while the exact details are unknown, the Farm Safety Partnership is committed to preventing any such accidents in the agricultural workplace.
We all know farming has an unenviable record of being the most dangerous industry in the UK. We have seen clear improvements, but these notifications should stop us becoming complacent.
Now in its 11th year, Farm Safety Week (17-21 July) is an opportunity to come together as an industry and recognise those lost to and impacted by incidents on farms. Whether new to the industry or in farming for years, we all have a role to play in improving our poor safety record. For one week a year, it is incumbent on us to focus on our responsibilities as farmers, farm workers, employees or contractors. Farm Safety Week aims to provide practical advice to make every day safe.
We know the industry has an attitude problem with health and safety, and many farmers ignore this aspect of their business until it is too late. To bring the issue to life, we find out what two CLA members are doing on their farms to manage risks ahead of this year’s harvest.
Newbottle Estate
Alice Townsend farms a mixed estate in Northamptonshire with the help of a stockman, shepherdess and tractor driver. A small team of gardeners also work on the estate. Alice is passionate about farm safety and considers herself responsible for setting the tone for her employees. Historic attitudes towards safety have not always made this easy, and in Alice’s experience, it takes years rather than months for this culture to bed in. Alice makes it clear to her employees that she is not willing to ever be in a position where she has to tell their family or relatives that they have had an accident.
Alice has found that health and safety terminology can be off-putting for her employees, so makes an effort to reframe the issue to make it easier to engage with. She has condensed the farm’s large health and safety file into a 20-page A5 handbook, given to each employee after induction. This includes pictures and diagrams on safe working, case studies on how injuries have occurred, emergency contacts and a map showing overhead cables and first aid kits. Employees are expected to be familiar with the content and are occasionally tested.
Alice also uses a health and safety consultant, who visits the estate four times a year. There is an annual meeting involving all estate staff, with a training component attached – for example working from heights or first aid. Staff are asked to identify what is most likely to injure them at work and what could be done to mitigate the risk. Alice then takes these suggestions away and writes to staff to explain how improvements will be made. A separate visit from the consultant comprises a mock Health and Safety Executive inspection, which includes in-person interviews with each employee.
Ahead of harvest, Alice will conduct her usual round of pre-harvest checks. This includes checking machinery and reviewing the driving licences and necessary qualifications of casual staff. At a pre-harvest meeting, danger points are identified and discussed so everyone is aware. Once harvest is underway, Alice provides all employees with a cooked meal in the evening, giving an opportunity for people to rest, refuel and talk about potential safety issues on the farm.
Alice says that, ultimately, staff appreciate they are being looked after.
Green Drove Farm
Jonny Kerr is a farm manager from Wiltshire. He works for the large farm contracting business Velcourt, which has a national health and safety policy for its 120 businesses. Each farm manager can tailor the policy to fit their business.
With harvest approaching, Jonny shared some of the steps he plans on taking to reduce the risks. Every employee must fill out a confidential health and safety questionnaire where they can disclose any health issues to help Jonny manage their work appropriately. Jonny puts a day of training aside for new staff members, which involves reviewing the health and safety policy in the office, and driving around the farm to identify hazards. For Jonny, it is about making each employee take responsibility for themselves, their employees and members of the public. During their first three weeks of employment, anyone who shows a poor attitude to safety can be dismissed within 24 hours.
Rather than asking harvest workers to start when harvest commences, Jonny gets them on farm in early July to help with pre-harvest work, such as preparing grain stores. This lets them slowly build up their work and become familiar with the farm, rather than starting in a chaotic way and putting time pressure on themselves to keep machinery working. Jonny makes it clear that it is his responsibility and not the harvest worker’s job to ensure the combine is running.
The company has a review process for reporting accidents and near misses. These are gathered centrally and then discussed at every farm’s weekly meeting.
Health and safety terminology can be off-putting, so make an effort to reframe the issue