Ripe results: how new innovations are helping a family farm
Jonathan Riley finds out more about Hugh Lowe Farms’ technological innovations to maintain the quality and improve yields of its soft fruits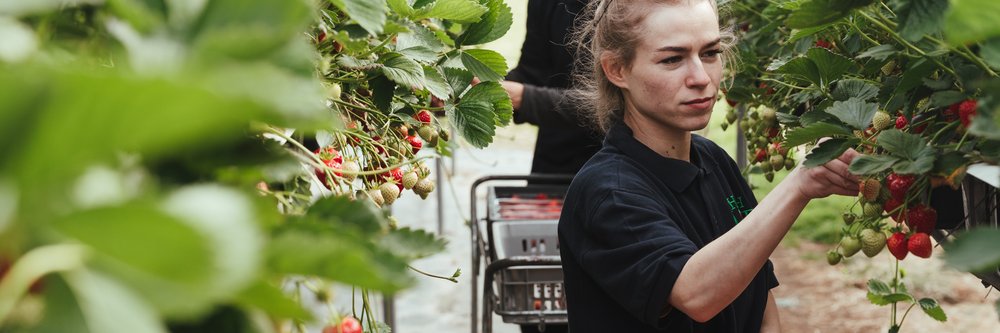
Technological and environmental innovation is central to the success and sustainability of a family farm in Kent.
The 720ha Hugh Lowe Farms, near Maidstone, grows 6,000 tonnes of soft fruit per year. Roughly a third of the farm is used for soft fruit, a third for arable and a third is managed for the environment. It sells fruit to major supermarkets and local premium outlets, and is Wimbledon’s sole supplier, providing about 1.5m strawberries a year.
Director Amelia McLean says the farm’s approach means that wild areas of wood, hedgerow and pasture are managed with a light touch to benefit biodiversity; arable growing areas and horticulture enterprises are farmed fairly intensively. ‘Intensively’ does not mean a reliance on chemical controls and fertiliser, referring instead to a precision approach based on rigorous data collection, technological and environmental innovation.
Technological innovations
Robotics
Hugh Lowe Farms has worked with robotics company Dogtooth Technologies for 10 years in trialling automated fruit picking. During last year’s harvest, a fleet of 60 robots identified ripe fruit, picked the berries and placed them into punnets. The machines run on caterpillar tracks and require one human supervisor for every 10 robots to oversee operations.
Amelia says the use of robots is in its infancy, and she cannot yet see a time when seasonal workers will be replaced completely. A problem is the relatively slow speed at which the robot assesses the quality of the fruit and picks it. She believes that pressure on labour availability will see robots become part of fruit-picking teams in the future.
While automated picking is still part of the longer innovative strategy, robots are already employed to control disease. The farm has a contract with Saga Robotics to provide an automated ultraviolet treatment that eradicates mildew. Robots shine UV light onto strawberry plants to destroy mildew spores. Fungicides are held in reserve as a last resort.
And the farm’s workshop has provided a less technical innovation: a mechanised drill to help staff plant strawberries. Motorised pickers’ trolleys, created by Dogtooth Technologies alongside Hugh Lowe Farms, are designed to make tasks easier for workers inside polytunnels.
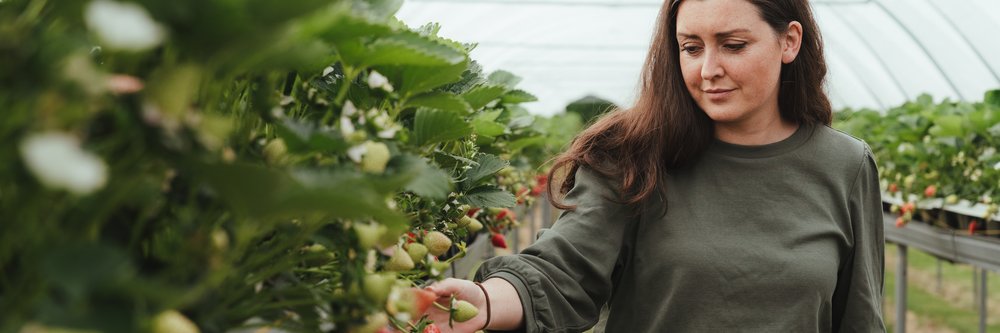
Sensors
Although fruit production has a high turnover, production costs and low prices mean margins are squeezed. This has focused attention and led to a drive to capture and analyse data using sensors.
Monitoring data extends down to each kilo of the harvested crop.
We monitor every input and output along with temperature and humidity inside polytunnels. We are data-obsessed
In fruit crops worth £200,000/ha, inputs and outputs are monitored down to the penny.
“We calculate irrigation rates used to achieve the crop, plant numbers required to hit kilos of fruit per hectare targets, picking rates, the level of non-harvest tasks, biological treatments and disease levels,” Amelia adds.
The farm is trialling a system that places a sensor on each picker’s trolley to assess the growing crop. Sensors use imaging technology and predictive algorithms to estimate yields, explains Amelia.
The artificial intelligence approach was originally part-funded by Innovate UK and allows a calculation of the likely output so the amount of wasted production can be reduced to a minimum.
Genetics
Meeting market demands is underpinned by the careful selection of the genetics required to hit buyer specifications. “We want to meet all of the requirements from taste and appearance but also need varieties with high kilo rates per plant,” Amelia says.
Selecting for disease resistance, meanwhile, cuts down crop losses and minimises the use of chemicals.
Environmental innovations
The company has adopted Science Based Targets initiative (SBTi) best practice measures and completed emissions assessments. SBTi promotes best practice in science-based target setting. From the base year of 2020, the farms are targeting a 42% reduction in greenhouse gas emissions up to 2030 by reducing inputs.
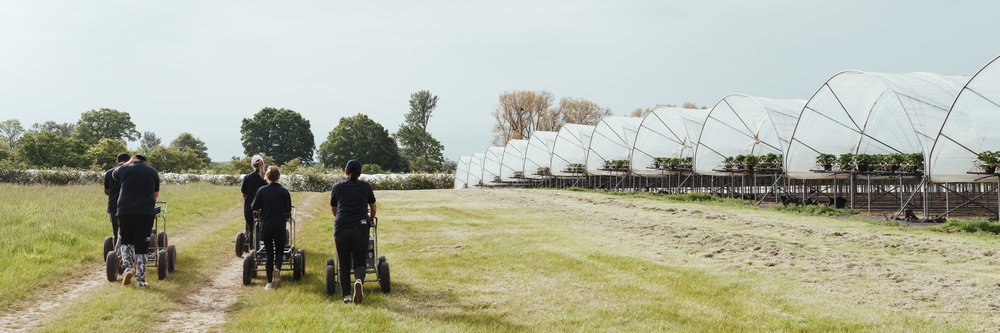
Biological pest control and pollinators
Biological controls are a key pillar of the farm’s environmental strategy. Predator insects are released into crops to tackle fruit pests. This has proved successful, with pesticide reduced to a backup policy.
In addition to limiting emissions, the reduction in pesticide use is designed to help pollinators thrive. The farm has 100 beehives to encourage pollination, and wildflower strips have been planted.
Water
Due to ever-increasing climate uncertainty, Hugh Lowe Farms has made signifi cant investments in water management and storage to capture up to 6,000m3 /ha/year from tunnelled sites. Systems are in place to recycle and retain water wherever it falls on buildings and polytunnels. Each polytunnel has a drainage system, and water is fed via a network of drains into reservoirs around the farm.
Energy use
Like most systems on the farm, data on energy use is collected and analysed against crop growth to control the optimum input and help prevent wastage. Energy is also generated via solar panels on buildings and is used to power irrigation pumps and onsite refrigeration.
The farm is also trialling the use of agri-voltaic strips. These are narrow flexible strips attached to polytunnel surfaces that can capture solar energy while allowing sufficient sunlight through to the crops.
“Our trials have shown that there is no negative effect on the growing crop, and energy is generated to power data collection stations and hopefully robots and other machines in the future,” says Amelia.
Recycling
The farm stopped using peat 15 years ago, and crops are planted in coir, a by-product of the coconut industry. It is now working with recycling company Recoir on an approach that composts and sterilises coir for reuse. Through this approach, crop output per litre of coir used has doubled.
Pots, posts, wires, rope and plastic polytunnel covers are all re-used. The polytunnels are built on earth floors rather than concrete, which reduces emissions associated with concrete hardstandings. After use, the frame can be disassembled and re-sited for further use while the ground returns to growing an agricultural crop.