The family farm growing a potato dynasty
Having recently celebrated a century of growing potatoes on its Northumberland farm, we speak to the Robson family about the CLA member’s farming and chipping operations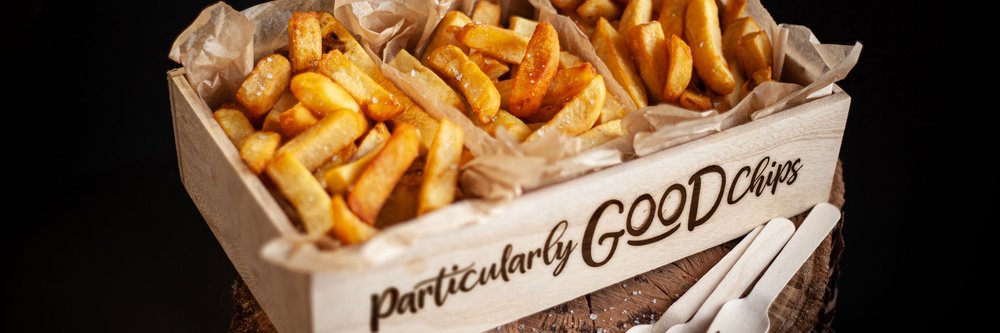
Potatoes have been part of the Robson family history for more than 100 years. The family, which grows the crop at Turvelaws near Wooler in Northumberland and Pressen Hill in the Scottish Borders, provides all the potatoes for Particularly Good Potatoes (PGP).
After completing his business degree and travelling around Russia and China, Mark Robson got involved in the family farming business with his father. He now farms 1,600 acres in-hand, with 270 acres managed in partnership and 350 acres of rented land.
Alongside arable farming, the business includes a chipping factory and a chicken enterprise focused on producing 12m bio-secure fertilised eggs per year.
Growing and chipping
The farm produces between 8,000 and 10,000 tonnes of potatoes annually, with three varieties grown for the chip factory: accord is ready in September and October, ramos from November to April and markies from May to August.
Mark says: “We had a trials day six years ago where we had 63 varieties and whittled it down to the top 10, and eventually our top three. We are continually trialing new varieties to ensure our own resilience.
“We also grow elland and king russet varieties for McCains, as well as charlotte salad potatoes for supermarkets distributed via Driffield-based Whole Crop Marketing.”
PGP chips around 40% of the farm’s potatoes, and half are distributed to the catering sector by DeliFresh. Mark, who was on the Potato Board prior to its demise, laments the sharp decline of potato farms. Around 19,000 farms have been lost since the 1970s; less than 1,000 remain.
The UK’s self-sufficiency in potatoes has declined from 100% in the 1970s to 65% today
Before setting up the on-farm chipping plant, Mark was horrified to discover that his local fish and chip shop imported its chips from Egypt. “It is insane to think the produce from Egypt was grown from seed potatoes that were originally exported there from Scotland. It is simply wrong on so many levels.”
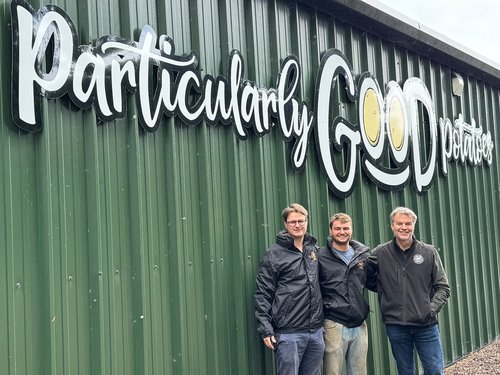
Adapting to change
Recognising that the market was changing, Mark looked into various potato-related products, such as vodka and crisps, but settled on producing chips, mainly for the catering industry. Production at the plant started in April 2019. A year later, Covid obliterated PGP’s orders to zero as hotels, restaurants and chip shops shut down.
Mark says: “Overnight, our order books dropped to zero. It had a severe impact on our cash flow but thanks to our understanding bank manager and government grants, we pulled through.
“Post-Covid, our cash flow remained unstable as the war in Ukraine and inflation resulted in high fertiliser and machinery costs. I would do anything for just a bit of stability.”
The farming operation has its challenges; for example, it is greatly impacted by the unpredictability of floods and droughts. But what frustrates Mark most are the bureaucracy, barriers and procrastination of government agencies on issues as diverse as addressing flooding or obtaining planning approval for something like a manure handling shed.
Carbon-neutral journey
Mark is keen to make the farming operation and chipping plant as sustainable as possible. Rebecca Maitland, PGP’s Marketing Manager, is taking the lead on making the operation carbon neutral over the next decade.
Rebecca says: “In December 2023, we undertook research to see what others are doing and to see what guidance and advice was available. In our quest, we are working with Agreena and Newcastle University to assess our inputs and outputs to measure progress. Environmental sustainability is also embedded within our workforce, as a crucial part of our work.
“Like many others in the land sector, we are still looking for the right calculators and methodologies to use.”
On the farming side, Mark stopped ploughing 10 years ago, which helps maintain the soil structure so it can absorb more water and lock in carbon. In addition, 600 acres of cover crops are planted to enrich the soil with nitrogen while sequestering carbon. The farm has 33,150 metres of hedgerows and 143 acres of land designated as a Site of Special Scientific Interest, enhancing the area’s biodiversity.
In the chipping factory, energy use and efficiency are key priorities, as is waste reduction. At a basic level, PGP is reducing its energy footprint by improving insulation and using more efficient lightbulbs and natural lighting. There is also the potential for solar panels in the future. All PGP packaging is FCA-approved and made from recycled plastic.
The biggest waste challenges are starch effluent and solid potato waste. The latter is sent to the farm’s neighbour at Doddington Dairy for use as supplementary livestock feed, while PGP has Environment Agency authorisation to decant some of the starchy water onto its farmland. Mark is looking at alternative applications for starch, which is often used in the pharmaceutical industry.
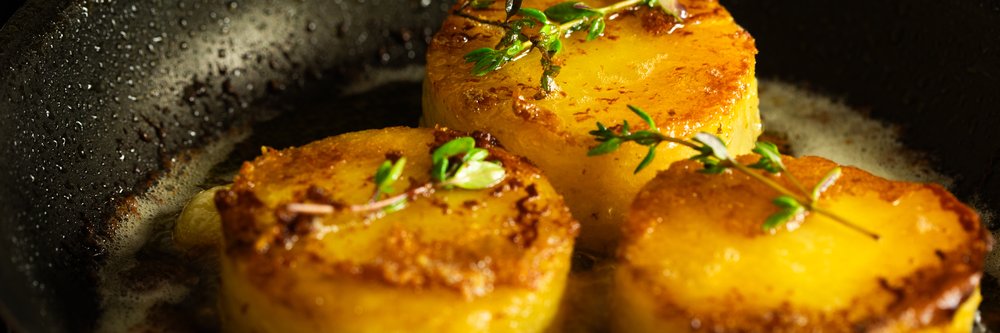
Future
Mark’s aim is to further consolidate and sustain the business. His sons William and Alastair and daughter Kitty are already actively involved, and he wants to leave the farm, environment and business in a better state than he found them.
Rebecca adds: “We want to continue building our brand so everyone can see what PGP is about and showcase that we are strongly rooted in our values of traceability, transparency and sustainability. In short, building the link between people and food.
“As part of our educational outreach work, we use our branded trailer and on-site polytunnel to host children, chefs, and suppliers for farm and factory tours. We’re also toying with the idea to launch a ‘don’t bin the skin’ campaign because potato skins are highly nutritious.”